

Thus, a less knowledgeable and capable person will ask more whys than a more knowledgeable and capable one.Ī third issue is that once a list of potential causes is generated, little is said about how to reduce the list without subjectivity. The advice I give is when by the answer you know what action to take to mitigate the effect. I’ve never seen anyone teach/explain when to stop digging deeper, i.e., when to stop asking why. It’s physical properties are due to ….? When have you reached the “true” root cause?īut often we just want to mitigate the effect, so we don’t need to get to root causes. The material’s fragility is due to physical properties. A leaky pipe maybe due to the material used. For example, a hole in a wall may be due to a leaky pipe. It’s not always possible to get to the “true” root cause.

Why does the material jam? Because it is out of spec. Why are there frequent line stoppages? Because the material jams. Application of the 5 Whys at this point can help drive the team to the root cause.
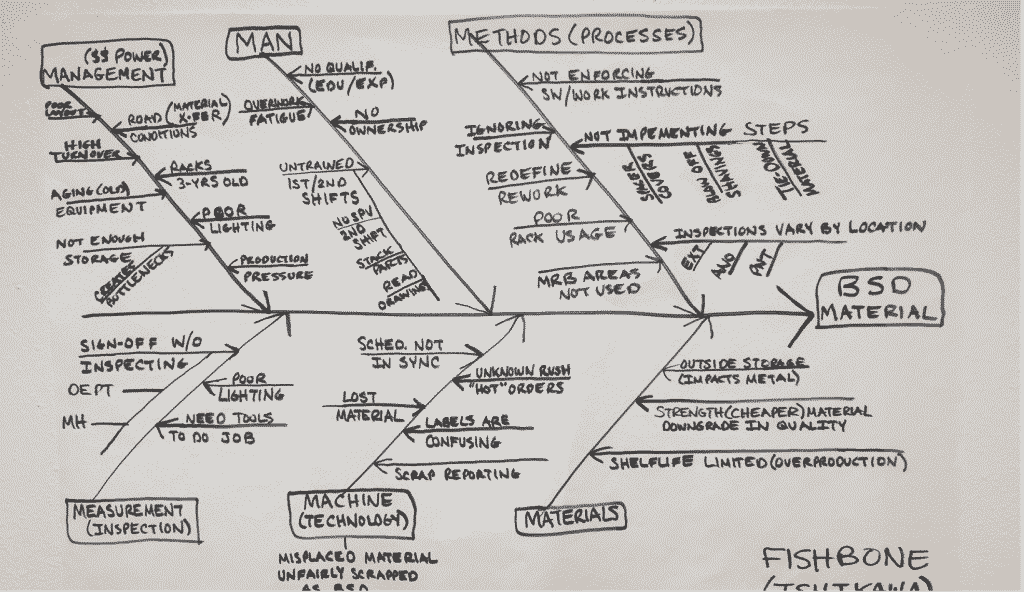
For instance, as shown in Figure 3, each cause coming off the main category “bone” could have one or more lines with sub-causes coming off of it. Sticky notes are particularly useful for this method – write one cause per sticky note and they are easily moved for grouping.Ī team is likely to find that once they have identified possible causes, they need to delve a little further to find a true root cause. For example, a possible cause of late deliveries of product XYZ within the Machine category could be “frequent line stoppages.”Īnother approach is to start by brainstorming the possible causes of the problem, and then determining appropriate categories based on what causes were identified. Team members – which should include subject matter experts and those who work within the processes related to the problem – then brainstorm the causes of the defined problem. This Lean Six Sigma tool can solve a basic problem that an organisation faces in daily life.įor Lean Six Sigma Training needs at ZaranTech, Visit. Once these factors are identified they can be eliminated and can result in coming on time to office. Hence an employee can try to control certain factors by identifying the reason for coming late to office. Rains, fog, Traffic jam and holidays can also affect the time taken by an employee to reach office.īasic materials like food, clothes, petrol and electricity may cause late coming to office. This type of analysis gives a clear picture for the situation.Malfunctioning of certain machines like alarm clock, coffee machines.Late while dropping the children to school.This is the lack of motivation through incentives at work.Waking Time and alarm clock malfunctioning.Method by which the employee comes to office.These are the factors which can affect the timing of an individual for office: So why does an employee come late to office? The causes can be identified with the help of fishbone analysis diagram. Repeated warnings and excuses have become a routine in an organization. Every company faces latecomers in their office. Now let’s see a practical example where this fishbone analysis diagram is used. By this technique we can identify the areas due to which the quality is not achieved.
ISHIKAWA DIAGRAM IN SIX SIGMA PROFESSIONAL
Fishbone analysis diagram is a simple tool that is used by Six Sigma professional to understand the root cause of a problem.

This tool helps to identify the cause for a problem.
